Multi-junction vertical-cavity surface-emitting lasers are likely to displace LEDs and edge-emitting lasers in sensing, finds Andy Extance
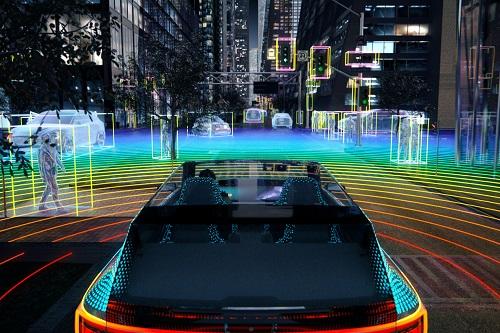
Ams Osram’s multi-junction VCSELs are helping to improve automotive lidar. Credit: Ams Osram
Five years ago, top-emitting vertical-cavity surface-emitting lasers (VCSELs) started lighting up people’s faces, and seemed destined to soon be driving around, widely illuminating our roads. That shining moment is yet to arrive, but more sophisticated multi-junction and mode and polarisation controlled VCSELs have now embarked towards this destination.
iPhone maker Apple’s face identification functionality transformed the VCSEL industry in 2017, explained Ralph Gudde, vice president marketing and sales, Trumpf Photonic Components in Ulm, Germany. ‘Apple paved the way in getting acceptance of VCSELs in smartphones,’ he said. ‘It started with a single VCSEL for proximity sensing, and we now have a handful to serve a variety of applications. A few other smartphone players like Huawei and Samsung have also adopted the technology. That is still the main driver in the VCSEL business in consumer electronics.’
From there, VCSELs seemed ready to leap into light detection and ranging, or lidar, for use in self-driving vehicles and driver-assist systems. Yet that journey has been slower than some may have hoped. That’s partly because there is ‘a good battle’ between better-established edge-emitting laser (EEL) diodes and VCSELs in this application, Gudde said.
But then, in 2020, a new multi-junction VCSEL technology entered the market. Multi-junction VCSEL arrays are already displacing existing devices, primarily LEDs, from sensing applications in smartphones and vehicles, and offer even better performance in automotive lidar.
Vixar, with headquarters in Plymouth, Minnesota and a subsidiary of Ams Osram, was the first company to commercialise multi-junction VCSEL technology. The technology involves forming two or more light emitting junctions in one device connected with a tunnel junction by epitaxially depositing GaAs-based semiconductor material, explained Dominik Schulten, segment manager, AR/VR and industry at Ams Osram. The junctions are more specifically known as PN junctions, named after the two layers they form an interface between. One layer contains GaAs with p-type doping with atoms such as magnesium, added to give it an overall positive charge. The other contains GaAs with n-type doping with atoms like silicon to give an overall negative charge.
Schulten explained that stacking multiple PN junctions allows VCSELs to better amplify optical power, increasing gain. As such, fewer distributed Bragg reflector layers must be deposited in VCSELs to trap light and enable laser gain. Removing these layers lowers a multi-junction VCSEL’s internal resistance, and therefore boosts efficiency in Ams Osram’s Powerboost products. ‘We are roughly reaching today 60 per cent efficiency on a single aperture VCSEL, and in an array 50 per cent,’ Schulten said. ‘That is 10-20 per cent higher than on a single junction VCSEL.’ This can obviously therefore reduce the electrical power needed to attain a particular optical power. Alternatively, it can increase optical power attainable with a particular electrical power input.
Multi-junction VCSEL technology wasn’t previously available because it requires epitaxially fabricating low resistance, low optical loss tunnel junctions that connect each PN junction. ‘In 2020, we started to get to a point where we feel comfortable to build something like that,’ Schulten said. But Ams Osram was motivated to do so because its customers were calling for higher power, more efficient VCSELs, Schulten added.
Arrayed advantages
Bringing many tiny multi-junction VCSEL chips together as different apertures in an array brings a further advance, Schulten explained, because it allows Ams Osram to optimise the driving current of each chip. ‘A single aperture can be ideally driven somewhere between 5-9mA,’ he said. ‘If you want to increase the power, you can't increase the current anymore, because then you would move out of the ideal efficiency or operating point. So, you just add another aperture.’
The improved power and efficiency combine with the original advantages VCSELs offer. These include fast pulse rates and switching times, Schulten said. Also, VCSEL wavelengths are stable, not changing much with temperature, and offer pulses spanning very narrow wavelength ranges. This helps minimise signal-to-noise ratios at the detectors in sensing applications, Schulten explained. That’s because to ensure the detector is only collecting light from the illuminator source, it must use a filter to remove distortion from other sources. The narrower the filter can be, the better the sensor performs. ‘That is advantageous for VCSELs because they don't move as much over temperature, and they are very narrow compared to LEDs and to EELs,’ Schulten underlined.
Multi-junction EELs had already been available from Ams Osram and other companies such as Saxonburg, Pennsylvania-based II-VI. But the advantages multi-junction VCSELs bring meant that II-VI also saw growing demand for the capabilities they offer in applications like 3D sensing and lidar, explained Gerald Dahlmann, the company’s director of strategic marketing for consumer electronics. II-VI can trace the origin of its VCSEL portfolio back to the very first such devices commercialised by Honeywell in Richardson, Texas, in the 1990s. ‘So, the engineering expertise required to design and manufacture such devices, and in particular the advanced epitaxy structures, was already available at II-VI,’ Dahlmann said. ‘So far, we have demonstrated devices with two, three, and five junctions.’
Dahlmann highlighted the increase in optical output power per unit area that stacking junctions brings. ‘Compared with conventional single-junction VCSELs, much higher peak power can be achieved with multi-junction VCSELs, which enables depth sensors and lidar systems with longer range, higher resolution, and better signal-to-noise ratio,’ he said.
II-VI also then combines multi-junction VCSELs into arrays to scale output power. ‘The VCSEL chips that we offer typically have between one and several hundred emitters,’ Dahlmann stated. ‘Additional benefits include the option to divide an array into several subarrays that can be switched on and off selectively.’ II-VI can also design arrays to provide specific patterns needed for techniques such as structured light or active stereo sensing.
Edging into competition
In April 2022, Lumentum, based in San Jose, also launched its M Series multi-junction VCSEL arrays for automotive, industrial lidar, and 3D sensing applications. Matt Everett, Lumentum’s director of product line management for 3D sensing noted that applications in vehicles are so important that ‘the “M” in the M Series stands for mobility’. Lumentum intends to replace EELs, the existing illumination source of choice, in existing mechanically scanned lidar systems or solid-state electronic scanning lidar systems.
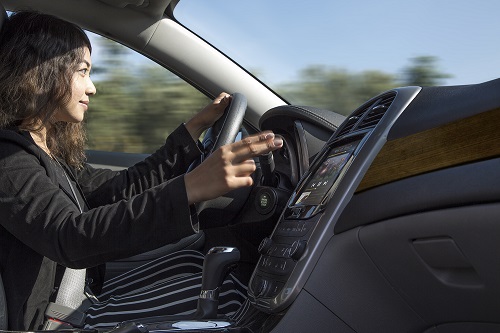
VCSELs can be used for in-car sensing such as gesture recognition. Credit: Lumentum
‘In some cases, this is because of a very specific need like high brightness from a very small source size, an aspect where EELs excel,’ Everett explained. ‘But more and more, due to the risk of failure in an EEL, and the complexity involved in these systems, with moving parts and weight added, alternative approaches like VCSEL-based solutions are being sought out and adopted. VCSELs are the path to truly solid-state electronic as opposed to mechanical systems.’
Lumentum VCSELs including the M Series and beyond are therefore being used in lidar for self-driving vehicles, including delivery robots and drive-assist, as well as factory and warehouse automation. They also enable or supplement data collection, transfer, and use within vehicles, and from vehicles to their environments, Everett said. A last important area is inside vehicles, to monitor drivers and other occupants, and recognise gestures. ‘For the first time, customers are taking advantage of the breakthrough technologies to develop and deploy compact, robust, and high-performing systems just as the market is demanding these application needs,’ Everett added.
Edge-emitting lasers and VCSELs both have their place in lidar applications, added Dahlmann, with II-VI having both product categories in its laser portfolio. ‘Edge-emitters have been available for a long time and are widely used in long-range lidar applications, where scanning systems currently dominate,’ he stressed. ‘VCSELs are relatively new in lidar applications, and only became a compelling alternative with the emergence of multi-junction technology.’ Dahlmann also agreed that the best fit for VCSELs is in flash or solid-state scanning lidar applications, specifically those ‘that are short- or medium-range, up to tens of metres of distance’.
Lidar is where the strengths of double- or multi-junction VCSELs play out, Dahlmann added. ‘To achieve adequate signal-to-noise ratio in bright daylight and at distances of several or even tens of metres, high optical output power is required, usually in very short pulses or bursts,’ he explained. Multi-junction devices achieve this, and retain VCSELs’ easy integration into modules and packages, and a circular beam shape that is advantageous in optical design.
Like Lumentum, Ams Osram and II-VI, Trumpf offers single- and multi-junction VCSEL arrays to achieve higher powers. But Gudde explained that Trumpf’s products also include proprietary structures that enable close control over polarisation and whether a device emits single or multimode light. ‘It's all aimed at providing customers better control of optical designs, as well as getting more stability of their system design of the sensing technology applied,’ Gudde explained. He noted that Trumpf first offered single mode VCSELs in 2005, and polarisation gratings the following year. ‘Even if we have never publicly communicated extensively that we have them, we have shipped tens of millions of single-mode VCSEL devices with polarisation gratings. Only lately, it became more obvious that this is of relevance. In the last two years, we have seen a lot of demand.’
Technology for everyday use
Monolithically integrating polarisation gratings within VCSELs rather than as separate devices makes systems smaller and simpler. ‘It's easier to mount one component than to do it with several components,’ commented Gudde.
Gudde also underlined growing interest in VCSELs for use inside vehicles, especially Trumpf’s 940nm arrays with polarisation gratings for time-of-flight sensing. This method illuminates objects repeatedly at a very fast rate, which again is VCSELs’ key strength, and measures the time taken for light to reflect or scatter back to a detector. It is especially useful for measuring distances and speeds. Getting the best depth resolution in time-of-flight means producing the shortest pulse possible, another of VCSELs’ main benefits.
‘It is still in a design-in phase to replace existing LED devices that are used for driver monitoring,’ he said. ‘There's not a car yet that has this device on board, but it’s a matter of a few years before those get to the market.’ More generally, a few high-end German and Chinese brands already use VCSELs in interior sensing, Gudde added. ‘Other than that, it is still a technology in early stages of evaluation, so needs a few more years of work to develop further.’
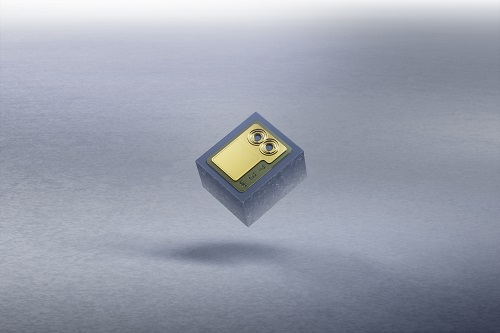
Trumpf produces a 940nm polarised VCSEL using a monolithically integrated grating. Credit: Trumpf
Meanwhile, in smartphones, Gudde observed that companies are trying to develop products where the sensors don’t obstruct the display. ‘As a consequence, all the sensing principles need to move under the display,’ he explained. VCSEL arrays enable that, for example Trumpf’s 940nm wavelength multimode device with polarisation grating, which can enable laser autofocus and proximity sensing. ‘We also see that customers are exploring longer wavelengths for under display sensing, and we are assessing those technologies as well,’ Gudde said.
Under display sensing is also one of Ams Osram’s key innovation focus areas, commented Schulten. ‘To this end, we believe that VCSELs especially will bring advantages in terms of reducing the signal-to-noise, again, thanks to the same principle as before, temperature stability and narrow wavelength beams,’ he said.
Schulten stressed that Ams Osram too receives many requests from long-established automotive companies and start-ups alike. ‘I guess it's because there's an increasing need for further detecting ranges, and closer observation around the car,’ he said. ‘There's a lot of need for sensors in cars, nowadays. And there's a strong belief that the VCSEL is fulfilling an important job going forward.’ In interior applications, Powerboost’s efficiency helps reduce power consumption, minimising the impact on a vehicle’s range, especially in electric vehicles. For exterior sensing, power is most important, Schulten stressed, which, as its name suggests, Powerboost can deliver.
Innovation in such areas is happening rapidly, Lumentum’s Everett underlined. ‘The new applications that are emerging every day are driving the growth and transformation of the VCSEL industry, as also are the industries and market segments in which VCSELs are used,’ he said. ‘We expect this innovation and application development to continue well into the future as the capabilities of these devices continue to develop and enable next-generation technologies for our everyday lives.’